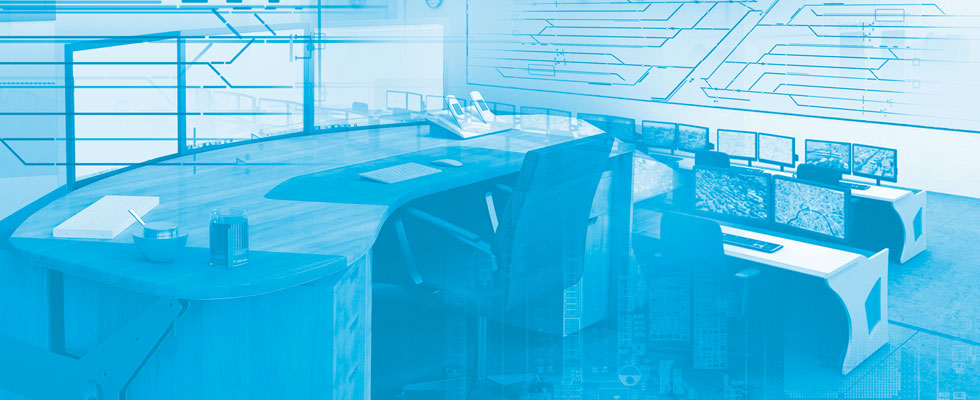
PRORAY SCADA centralized traffic control system is a software package intended to collect, process, display and archive information about train traffic and its control.
Software package is operated under QNX real time operating system intended for embedded systems. QNX operating system is transferred to many platforms and can be operated on any modern processor that is used with embedded systems.
Proray SCADA provides:
- collection and analyze of data received from system trackside assets (points, traffic lights, point sensors, etc.);
- signal state visualization;
- keeping history and archiving of system states, signals and emergency situations;
- system objects centralized control from operator’s automated work place;
- reliable and safe data transfer to the operations control center;
- access right differentiation and access authorization to the data sources and control
facilities.
System Composition
Station Level
Station level includes operator’s automated work places (AWP) and set of station servers intended to receive, process and store the information from trackside assets. Station level includes operator’s automated work places (AWP) and set of station servers intended to receive, process and store the information from trackside assets.
Operations Control Center Level
Operations control center level comprises operator’s AWPs as well as system configurator’s AWP, communication equipment with station level, video wall and data base server intended to collect and store configuration of system elements as well as system state history.
System Components Structure
ProRay SCADA system includes such components as client, data base server, node server and devices.
Client is a part of the system that provides interaction with users and comprises video wall, which displays general information about the state of all system elements as well as operator’s AWP, which displays information about certain system components and controls them.
Data base server is a part of the system that ensures storage and provides information about sequence of states and settings. It includes configuration data base of the system elements, data base of the system elements history as well as history collection client i.e. current state of the system elements.
Node server includes data base server and logic server, history collection module, Modbus RTU device driver, Modbus TCP device driver and Custom additional device driver.
System devices include Modbus RTU device, Modbus TCP device, Custom additional device.
To realize interaction between the users and the hardware the system includes the following components:
- users who follow up complex changes in hardware device states and if necessary control them;
- terminal that provides user friendly interface of interaction between users and hardware devices.
Terminals include the following software components:
- state display module that shows the users current state of hardware and logic elements of the system;
- state history display module shows the users history of state changes of the system hardware and logic elements;
- state control module allows the users to set (change) the state of system hardware elements;
- authentication module is a system of verification and differentiation of user’s access rights to different system control functions.
Servers are intended to receive, process and accumulate the information from hardware devices and terminals. Servers perform the following functions:
- Data analyze and collection. Servers process and accumulate data from hardware and logic components of the system.
- Control of the system hardware devices. Servers collect, process and transmit the commands to the hardware components of the system.
- Configuration of the system components. Servers process and store setting changes of hardware and logic components of the system.
- Accumulation and processing of change history. Servers collect and process state history of logic and hardware components of the system.
Advantages of Proray SCADA System Implementation
High Information Capacity and Reliability
System implementation allows to analyze large amounts of information about system device status suitable for archiving.
Analyze of Operator’s Actions
Keeping the history of the system device status allows to analyze operator’s actions, define mistakes and correct them.
Improving the Quality of Operator’s Work
User friendly interface of the system allows to decrease the level of tiredness and increase accuracy of operator’s work.
Adaptability
This system is open and extensible. It can be connected to any types of electric interlocking system. The system is easy to adapt at the design stage as well as at its modernization stage during the operation.