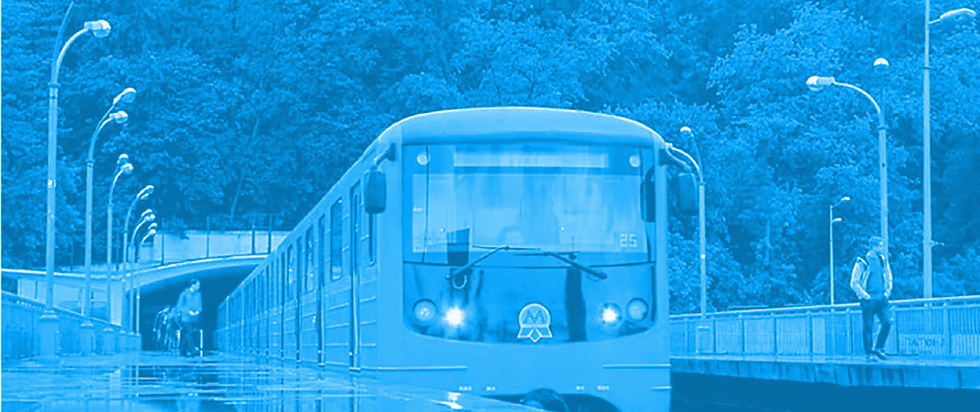
The system continuously monitors the temperature of the axle bearings of each car and timely transmits information about the heating level during movement.
The system is designed to prevent accidents in a timely manner and replace the outdated distance system of remote monitoring of the condition of the axle bearing of subway cars.
The system contains:
- Wireless electrically independent temperature measurement sensor „TERMIT“.
- Car controller „TermoGUARD“.
- Display controller in the driver’s cab „ThermoALARM“.
- Station controller „ThermoLOGIC“.
- Software „ThermoPiLOT“.
- Software „Chief engineer workstation“.
Sensor, installed directly at the axle box, continuously measure the temperature and transmit information about the temperature, signal level and voltage of the internal battery to the car controller via a radio channel.
Car controller «TermoGUARD» collects data by radio channel, measure the ambient temperature, processes and transmits the data to the TermoALARM display controller in the driver’s cab, and then the information is transmitted via the radio channel through the station controller to the underground network and stored in the cloud database.
To control the current values of the temperature of the axle bearings, the workstation in the OCC „TermoPiLOT“ is used.
For the dynamics of axle bearings heating, analysis of the wear rate, forecasting of the residual life and planning of repairs, the workstation of the „Chief engineer workstation“ is used.
In the event of an emergency heating of the axle bearing, the system generates an audible and light signal indicating the number of the train car and the wheel set on the car at the OCC workstation and on the display controller in the driver’s cab.
High measurement accuracy – modern high-precision analog-digital elements are used, high-precision measurement directly at the axle box. Optionally, it is possible to measure the oil temperature in the axle bearing.
High reliability of the system – the failure of one sensor leads to the upsent of monitoring of only one axle box. The failure of the station controller or communication lines with control centre doesn’t fluence to the working of the whole system (all data store in the car controllers).
Prompt response to overheating – the system provides information about overheating directly to the driver’s cab for prompt response. The axle bearing temperature and ambient temperature are measured continuously on each car throughout the entire line, which makes it possible to take into account the temperature difference anywhere on the line.
Heating dynamics control – the system provides for automatic registration and storage of data on the temperature of each axle bearing, the environment on each car, and the supply voltage of the sensor battery. This allows to follows the dynamics of heating, timely detect heated axle bearings before the onset of emergency heating, detect false heating from the actual one, and also plan repairs and maintenance.
Remote diagnostics – the system includes tools for remote diagnostics in the car controller, in the driver’s cab and at the chief engineer workstation. The current state of the system is shown at the related workstation in the OCC.
High maintainability and ease of maintenance – the sensors are mounted using a standard bolted connection. There is no track equipment in the system. There aren’t mechanical moving parts with electric drivesIn a system. The system does not require constant maintenance. If necessary, the sensor battery can be replaced within a few minutes. System maintenance does not require highly qualified personnel.